Commitment to Quality
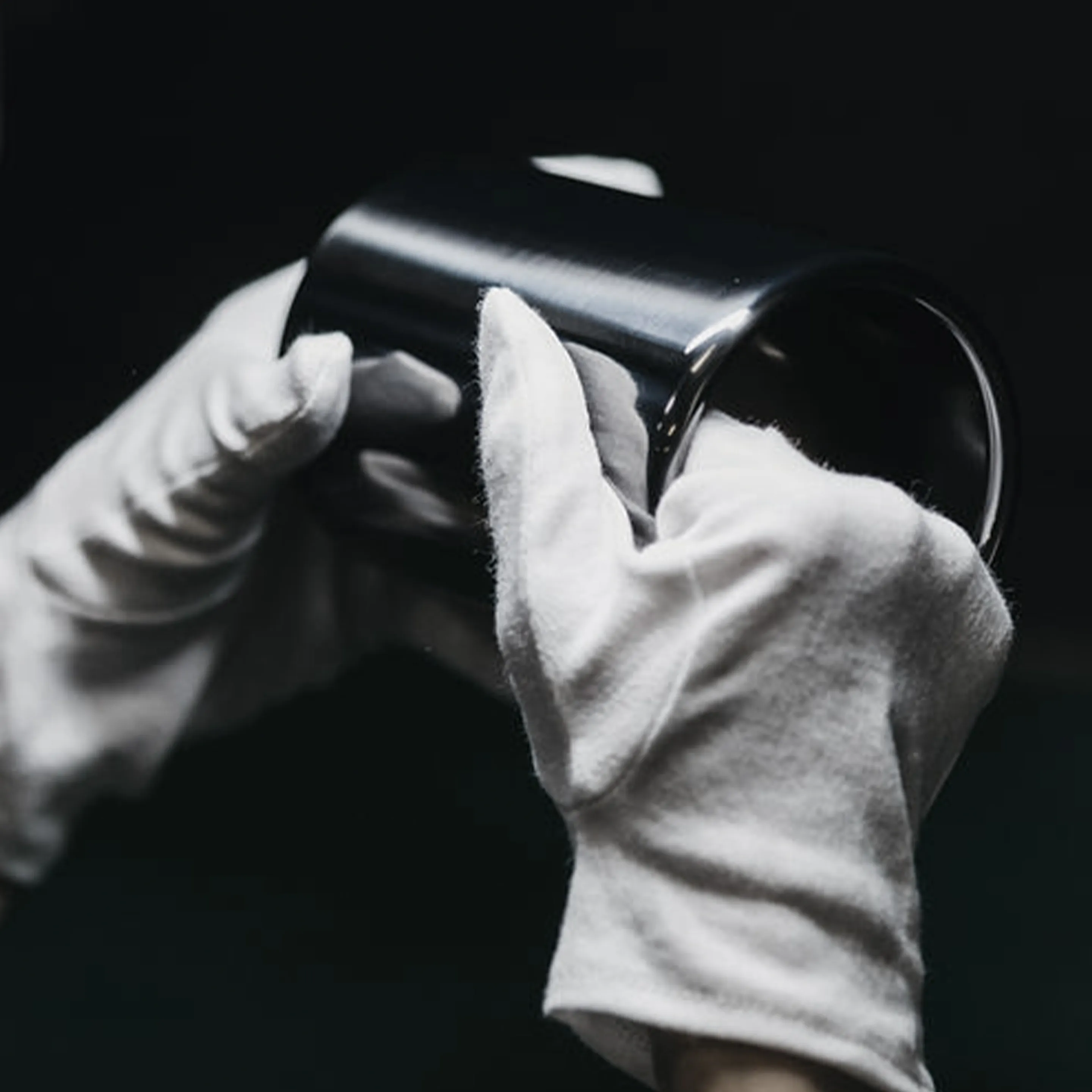
We ensure thorough quality control throughout the entire process, from product receipt to shipment, based on data. Using digitized work instructions and process manuals, we simplify data access, reduce work variability, and standardize quality control. Additionally, by collecting and analyzing quality data in real time, we make more accurate and rapid quality-related decisions.
We store processing condition data, such as vacuum levels, processing temperatures, gas flow rates, and coating times, in a digital database for easy search and analysis. Strict management of processing conditions and traceability are at the core of our quality management and are essential for sustainable business operations.
In the manufacturing process, we have established standard operating procedures (SOPs) to ensure all workers perform tasks consistently. This enables us to produce products with stable, consistent quality.
We place a strong emphasis on employee education and training. By raising awareness of quality and mastering the latest technologies and inspection methods, we aim to enhance the overall quality of the manufacturing process.
We establish stringent inspection standards for each product to ensure quality that meets our customers' requirements. These standards are customized based on specific customer demands.
Providing stable quality and earning trust are our top priorities, and the inspection process is key to this. Our inspectors are responsible not just for the products but also for NCC's reputation. Through thorough inspections, we secure our customers' trust.
By quickly relaying inspection results to the processing department, we maintain a continuous process of quality improvement. Timely sharing of inspection results helps identify issues early in the processing stages, minimizing the occurrence of defects.
We take great joy in seeing our improved technology reflected in our products and making a positive impact on society by finding them in the market. Enhancing the appearance of our products and increasing customer satisfaction gives us a sense of achievement and fulfillment. Our quality management and inspection systems are crucial for ensuring product reliability and customer satisfaction. By proactively committing to quality, all our employees ensure that we consistently deliver the highest quality products to the market.
Business Hours: Weekdays 8:30 AM - 5:30 PM